OK, I have been doing a bunch of reading about the highly innovative approaches to energy management being tested in places like Arizona. Phoenix as you can imagine sees temperature extremes like few other places in the country. (I remember stepping off a plane at Sky Harbor Airport in June 1979 and seeing an air temperature of 118-degrees). HEAT is a major topic in Phoenix. And as they say, "It's a dry heat". That said, it is a great place for people and academia and technology. Lots of land, lots of great people, lots of sunshine.
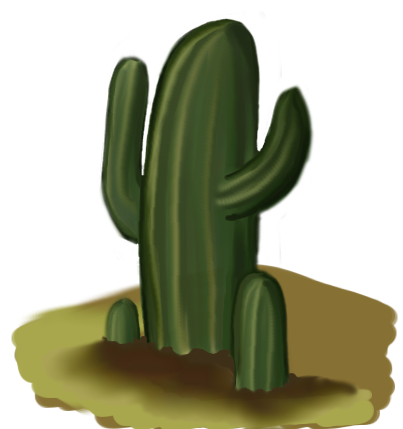
So it was no wonder that a 'master plan' was created when revitalizing their economy over the past decade. New headquarter locations, businesses, downtown campuses and sprawling Data Centers have all sprung up and are considered some of the best in the nation. (Look at I/O Data Center's North 48th street facility as an example of a BIG new data center, with HALF A MILLION square feet coming online).
For the downtown area, an innovative approach was taken in the 2002 timeframe for cooling which I had not seen at this scale before. The local public utility (APS) created a commercial partnership called Northwind to provide cooling to the new sports stadium being built. Traditional approaches for cooling this size open-air pro sports stadium in 120-degree heat proved to be an interesting challenge, so innovative new ways of doing so were solicited. The challenge: Provide a comfortable environment for tens of thousands of sports fans during a ball game being played in the hot July and August afternoons. Somehow exploit the fact that lots of extra capacity in POWER was widely available during the middle of the night when kilowatt rates were low, and be prepared for massive cooling needs during the next DAY (about 12 hours later). The Opportunity: Figure out how to spend money on energy 12 hours before it was needed? How to STORE energy required for cooling at this scale effectively. They needed a massive 'energy battery'.
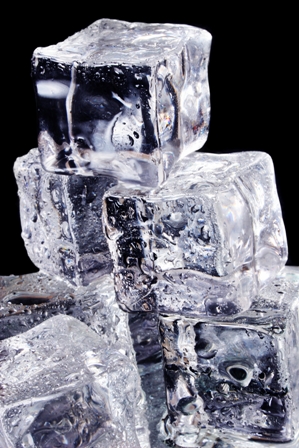
So, how did they solve this energy management task? ICE. It occured to their engineers that ICE is a great medium for storing energy. It can be created at any time, and used in the future as demand requires. Ultimately they built a highly efficient ICE plant that each night was able to manufacture 3 MILLION POUNDS of solid ICE when the power rates were the lowest. As each subsequent day progressed and business demands required cooling, the ICE would be used to absorb heat from water with the newly chilled water distributed as needed. The water was recaptured, and used to create ICE the next night in a closed loop system.
This approach worked SO well, that within the first few years, Northwind had sold it's entire energy savings capacity for the downtown plant to other commercial properties in the area. Turns out it really is quite easy to transport this chilled water at a relatively low cost in an area such as downtown Phoenix. Economies of scale play out nicely here.
Who would have thought? Make lots of ICE at midnight when it was cheap, and then use it to cool as needed the next day. And do so on a REALLY GRAND scale to the tune of MILLIONS of pounds each day. Actually there are a number of projects just like this now in operation, including several in New York City and Toronto to name a few.
Energy management innovation is key. Look past the traditional. Investments were made in well thought-out new technologies that could capture savings and return value to customers. Everybody Wins!